Warehouse Solution Storage Mezzanines
Warehouse Solution Storage Mezzanines is a common storage method that significantly increases storage capacity by making full use of vertical space, especially in scenarios where the warehouse area is limited or you want to maximize inventory storage density. This solution not only effectively adds additional storage layers within the existing building structure, but also helps companies improve space utilization without expanding the floor space, thereby optimizing warehousing processes, improving operational efficiency, and leaving more flexibility for future expansion.
1. Core advantages of Warehouse Solution Storage Mezzanines
Efficient use of space
When the warehouse height allows, add multiple layers of storage space by building mezzanines to increase storage density per unit area.
Suitable for storing light or medium-weight goods (such as packaging materials, electronic products, spare parts, etc.).
Flexible partitioning
The mezzanines can be divided into different functional areas (such as temporary storage, picking area, office area or equipment storage area).
Cost-effectiveness
Compared with expanding the warehouse or renting a new site, the initial investment for mezzanines is lower.
2. Key considerations for Warehouse Solution Storage Mezzanines
Structural safety and load-bearing
Material selection: steel structure (lightweight, quick to install), concrete (high load-bearing but long construction period) or modular structure.
Load capacity: needs to be designed according to the weight of the stored goods (light mezzanines usually bear 300-500kg/㎡, heavy ones can reach more than 1 ton).
Compliance: needs to comply with local building regulations and be reviewed by structural engineers.
Storey height and channel planning
The height of the mezzanine must meet the needs of personnel or equipment passage (generally the net height of the lower floor is ≥2.5 meters, and the height of the mezzanine is ≥2.2 meters).
Reserve forklifts, AGVs or personnel channels to ensure logistics efficiency.
Fire and safety
Install fire sprinkler systems, emergency lighting and escape routes.
Guardrail height (usually ≥1.1 meters) and anti-slip floor design.
Scalability
Modular design facilitates future adjustments or expansions.
3. Common mezzanine types and applicable scenarios
Features of steel structure mezzanine: lightweight, fast installation, low cost; applicable scenarios: light cargo storage, temporary expansion
Features of concrete mezzanine: high load-bearing capacity, strong durability; applicable scenarios: heavy equipment storage, long-term use
Features of loft-type shelves: integrated with shelves, flexible stratification; applicable scenarios: small item picking (e-commerce, parts warehouse)
Features of combined mezzanine Steel frame + steel plate structure, balance cost and load-bearing capacity; applicable scenarios: medium-sized warehouse transformation
4. Implementation process recommendations
Demand assessment
Clearly store the type, weight, and frequency of goods in and out of the warehouse.
Measure warehouse net height, column spacing, ground load-bearing capacity and other parameters.
Scheme design
Work with a professional team to develop structural drawings and fire protection plans.
Plan the flow of goods (such as elevators, conveyor belts or ramps connecting mezzanines).
Construction and acceptance
Select compliant materials to ensure that the construction meets safety standards.
Carry out load testing and fire protection acceptance after completion.
5. Potential Challenges and Responses
Cost Control: Modular design can reduce the cost of later adjustments.
Spatial Depression: Reasonably design the floor height, increase lighting and ventilation.
Equipment Limitation: Large forklifts may not be used in the mezzanine area, and light handling tools (such as electric pallet trucks) can be used instead.
6. Combination of Intelligent Warehousing Technology
Automated Storage and Retrieval System (AS/RS): The mezzanine is integrated with automated shelves to improve sorting efficiency.
Internet of Things (IoT) Monitoring: Install sensors to monitor mezzanine load, temperature and humidity data.
By rationally planning the storage mezzanine, companies can significantly improve their storage capacity without expanding the floor space. It is recommended to give priority to modular and scalable designs to adapt to future business changes. If further optimization is required, shelf systems or automation technology can be combined to achieve higher efficiency.
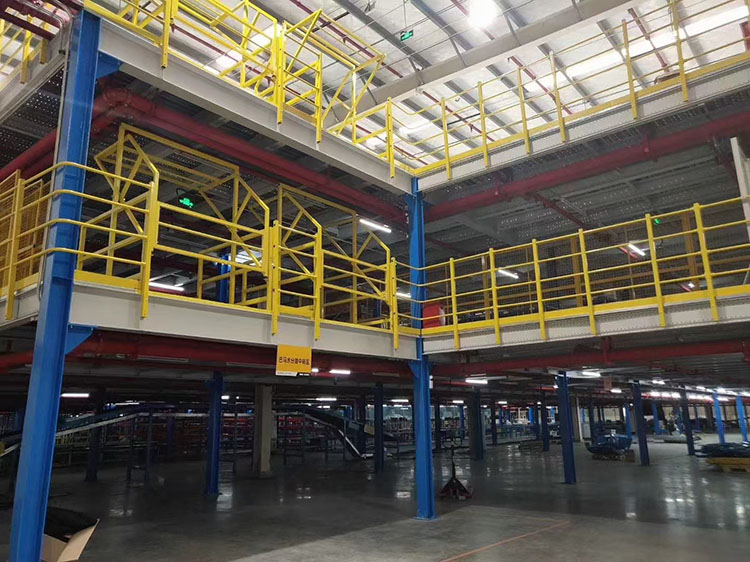
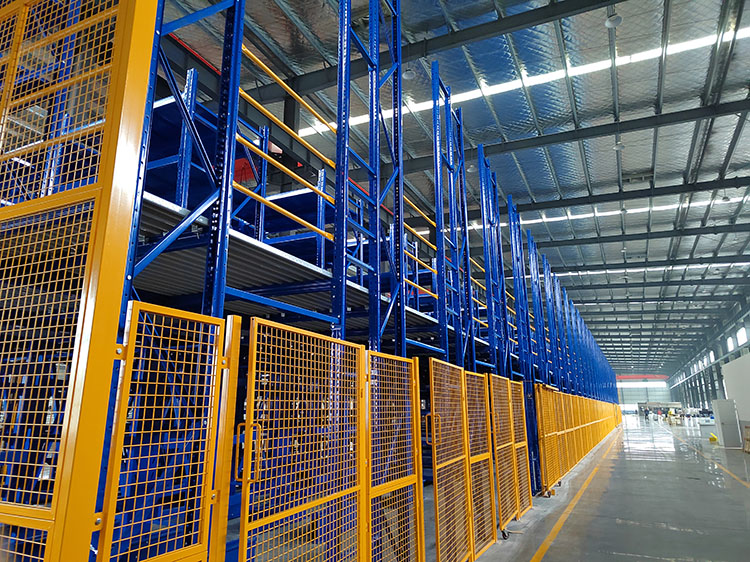
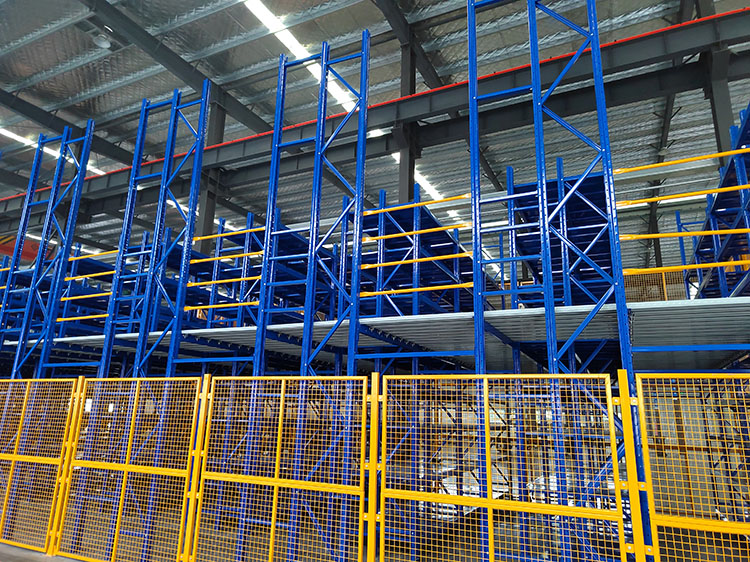
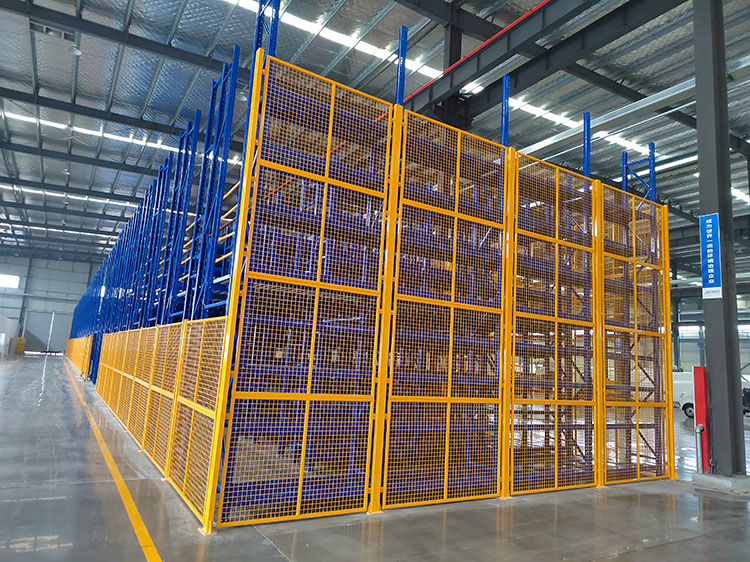
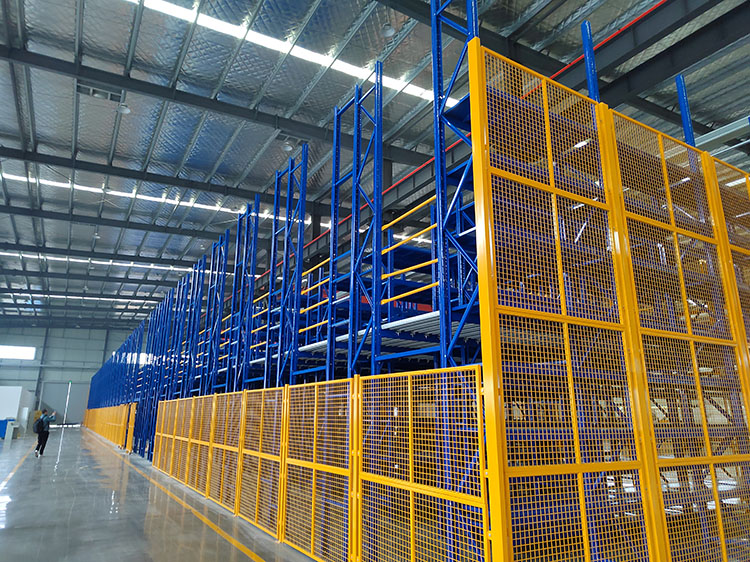