Push Back Racking System in Warehouse
Push Back Racking System is a high-density storage solution designed to maximize warehouse space by allowing multiple pallets to be stored in a single lane. Operating on a Last-In, First-Out (LIFO) principle, this system utilizes inclined rails and nested carts, enabling forklifts to load and retrieve pallets from the same aisle, thereby enhancing operational efficiency and space utilization.
Specifications
Storage Depth: Typically accommodates 2 to 6 pallets per lane.
Lane Configuration: Each lane is dedicated to a specific SKU, facilitating organized storage.
Loading/Unloading: Conducted from a single aisle, reducing the need for multiple access points.
System Type: LIFO (Last-In, First-Out), suitable for products with medium turnover rates.
Weight Capacity: Varies based on design; systems are engineered to support heavy loads per level.
Materials
Frames: Constructed from high-strength steel, featuring uprights with cross-sectional dimensions up to 120×95 mm and thicknesses ranging from 1.5 to 3.0 mm.
Crossbeams: Front, middle, and rear crossbeams with thicknesses up to 2.0 mm enhance structural stability.
Guide Rails: Made from 3.0 mm thick steel pipes, facilitating smooth movement of carts.
Carts: Fabricated from 2.0 mm thick high-quality channel steel, equipped with top-tier bearings for reliable operation.
Safety Components: Includes 4.0 mm thick front beam stoppers and 300 mm high, 4.0 mm thick U-shaped frame protectors to prevent damage from forklift operations.
Advantages
Space Optimization: By reducing aisle space, warehouses can store 25–30% more pallets within the same footprint.
Operational Efficiency: Single-aisle loading and unloading streamline forklift operations, decreasing handling time.
Enhanced Safety: Forklifts do not enter the racking structure, minimizing the risk of accidents and equipment damage.
Low Maintenance: The robust construction ensures longevity with minimal upkeep.
Flexibility: Accommodates various pallet sizes and weights, making it adaptable to diverse inventory needs.
Applications
Warehouses with Medium-Turnover Products: Ideal for storing goods that require efficient space utilization without frequent access.
Cold Storage Facilities: Suitable for environments with temperatures ranging from -30°C to 40°C, aiding in energy conservation by reducing the volume to be cooled.
Retail and Distribution Centers: Effective for managing a variety of SKUs with moderate turnover rates.
Manufacturing Plants: Supports storage of raw materials and finished goods in a compact footprint.
Buffer Zones for Order Picking: Serves as temporary storage for prepared orders awaiting shipment.
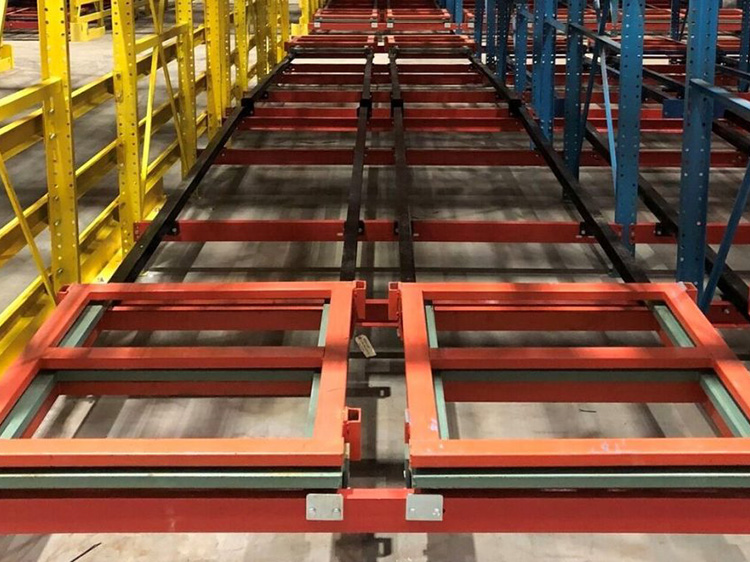
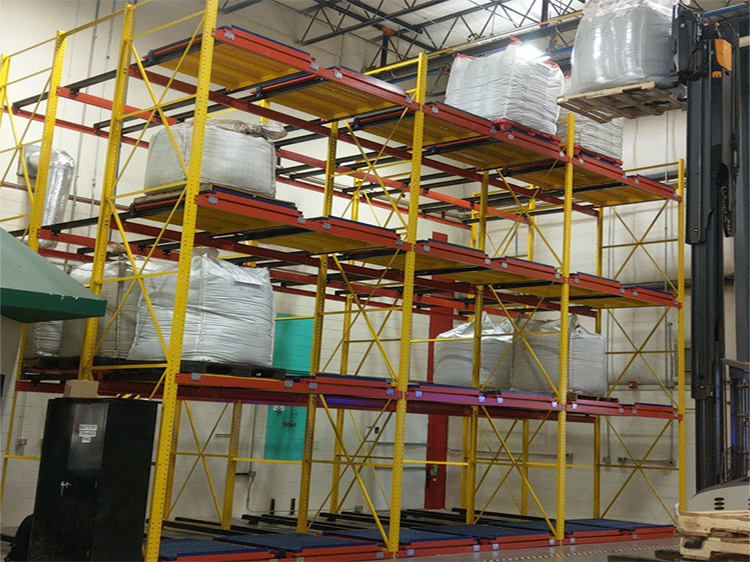
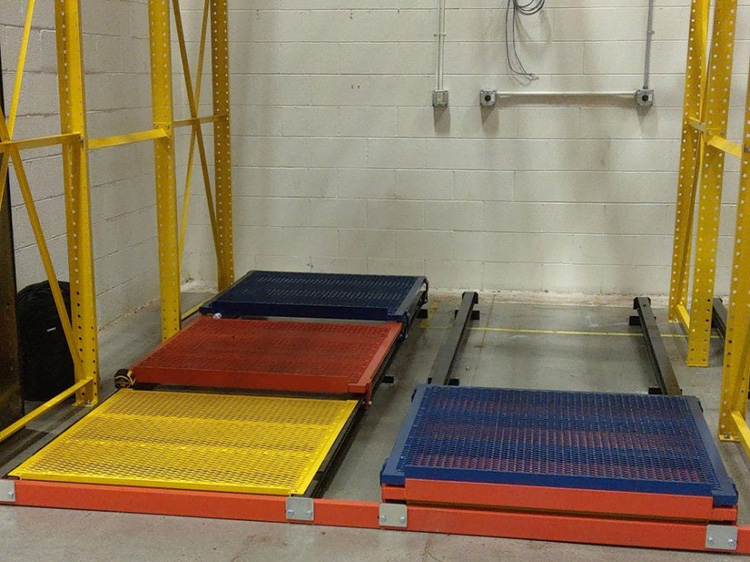